When it comes to construction and structural engineering, the selection of the right rebar gauge is crucial. Rebar, or reinforcing bar, is essential for providing tensile strength to concrete structures, ensuring durability and stability. This guide aims to simplify the process of selecting the appropriate gauge for your specific project needs, whether you’re a seasoned professional or a DIY enthusiast.
Understanding Rebar Gauges
Reobar is available in various gauges, which refer to the thickness of the bar. The gauge of rebar is typically measured in millimetres, with common sizes ranging from 6mm to 32mm. The choice of gauge directly impacts the structural integrity of the concrete, making it essential to understand the implications of each size. The selection process can often be daunting, especially for those new to construction or DIY projects, as the right gauge not only influences the strength but also the durability and longevity of the structure being built.
What is Gauge?
Gauge is a term used to denote the diameter of the rebar. In the context of rebar, a higher gauge number indicates a thinner bar, while a lower number signifies a thicker bar. For example, a 16mm rebar is thicker than a 10mm rebar. This measurement is critical as it affects the load-bearing capacity and overall strength of the concrete structure. Additionally, the gauge can influence the ease of handling and installation; thicker bars may require more effort to bend or cut, while thinner bars can be more manageable but may not provide the same level of support.

Common Rebar Sizes and Their Uses
The most commonly used rebar sizes include:
- 10mm: Often used for light-duty applications such as garden walls and small slabs.
- 12mm: Suitable for residential foundations and driveways.
- 16mm: Ideal for medium-sized structures, including commercial buildings.
- 20mm and above: Typically used for heavy-duty applications such as bridges and high-rise buildings.
Each size serves a specific purpose, and understanding these applications will help in making an informed choice. For instance, while a 10mm rebar may suffice for a simple garden wall, a 20mm rebar is essential for ensuring the stability of a multi-storey car park. Furthermore, the choice of rebar size can also depend on environmental factors; areas prone to seismic activity may require larger gauges to withstand the forces exerted during an earthquake. The interplay between gauge size and environmental conditions underscores the importance of careful planning and consideration in construction projects. Learn more about environmental at https://www.epa.gov/education/what-environmental-education
Factors to Consider When Selecting Rebar Gauge
Selecting the right gauge of rebar involves several considerations. Factors such as load requirements, environmental conditions, and project specifications play a significant role in determining the appropriate size.
Load-Bearing Requirements
One of the primary factors to consider is the load-bearing capacity of the structure. Heavier loads necessitate thicker rebar to ensure that the concrete can withstand the stress. Engineers typically calculate the expected loads and choose a gauge that meets or exceeds these requirements. For instance, a building designed to support heavy machinery will require a larger gauge than one intended for residential use. Furthermore, it is essential to account for dynamic loads, such as those caused by wind or seismic activity, which can significantly impact the structural integrity. In such cases, a thorough analysis using advanced engineering software can help determine the most suitable rebar gauge, ensuring safety and longevity.
Environmental Conditions
The environment in which the concrete will be placed is another critical factor. In areas prone to corrosion, such as coastal regions, using thicker rebar or corrosion-resistant materials may be necessary. Additionally, extreme temperatures can affect the performance of concrete and rebar, making it essential to consider the local climate when selecting the gauge. For example, in regions with frequent freeze-thaw cycles, the risk of cracking increases, necessitating the use of rebar that can accommodate such stresses. Moreover, exposure to chemicals, such as those found in industrial settings, may also dictate the choice of rebar, prompting the use of epoxy-coated or stainless steel options to enhance durability.
Project Specifications and Standards
Every construction project is unique, and adhering to local building codes and standards is vital. These regulations often dictate the minimum requirements for rebar gauge based on the type of structure and its intended use. Consulting with a structural engineer or referring to local guidelines can provide clarity on the appropriate gauge for your specific project. Additionally, it is worth noting that different countries may have varying standards, so understanding the specific requirements of the region is crucial. For instance, the British Standards Institution (BSI) provides comprehensive guidelines that outline the necessary specifications for rebar in various construction scenarios, ensuring that safety and quality are maintained throughout the building process. Engaging with these standards not only aids in compliance but also fosters best practices in construction, ultimately contributing to the overall success of the project.
Benefits of Using the Correct Rebar Gauge
Choosing the correct gauge of rebar offers numerous benefits, including enhanced structural integrity, longevity, and cost-effectiveness. Understanding these advantages can help in making a more informed decision.
Enhanced Structural Integrity
The primary purpose of rebar is to provide tensile strength to concrete. Using the correct gauge ensures that the structure can withstand the forces it will encounter over its lifespan. Thicker rebar offers greater resistance to bending and breaking, contributing to a more robust and reliable structure. Furthermore, the proper gauge of rebar can also help to distribute loads more evenly throughout the concrete, which is particularly important in high-stress applications such as bridges and high-rise buildings. This careful load distribution can prevent localised failures, which may compromise the overall safety and functionality of the structure.
Increased Longevity
Structures built with the appropriate gauge of rebar are likely to last longer. This longevity is particularly crucial in areas exposed to harsh environmental conditions. By selecting the right gauge, the risk of structural failure due to corrosion or stress is significantly reduced, leading to fewer repairs and replacements over time. Additionally, using the correct gauge can improve the overall durability of the concrete itself, as it can help to prevent cracking and spalling that often occurs in inadequately reinforced structures. This is especially relevant in coastal regions where saltwater exposure can accelerate deterioration, making the choice of rebar gauge a vital consideration for long-term structural health. To read about deterioration click here.
Cost-Effectiveness
While it may be tempting to opt for a thinner gauge to save on costs, this decision can be short-sighted. Using insufficiently sized rebar may lead to structural issues that require costly repairs down the line. Investing in the correct gauge from the outset can save money in the long run by reducing the need for maintenance and ensuring compliance with building regulations. Moreover, a well-designed structure with the right rebar gauge can enhance the overall efficiency of the construction process, as it may reduce the time spent on rework and inspections. This efficiency not only translates to financial savings but also contributes to a smoother project timeline, allowing for timely completion and minimised disruption to surrounding areas.
How to Measure Rebar Gauge
Measuring the gauge of rebar is a straightforward process, but accuracy is vital. Here’s a simple guide to measuring rebar gauge effectively.
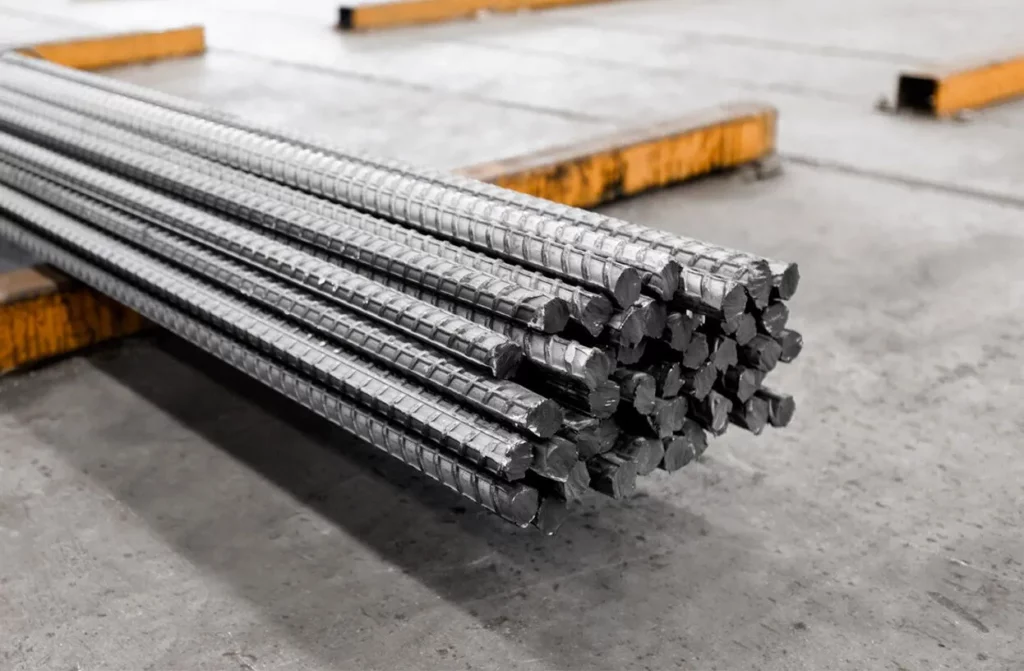
Tools Required
To measure rebar gauge, you will need:
- A caliper or measuring tape
- A ruler (if a caliper is not available)
Steps to Measure
- Place the caliper or measuring tape around the rebar.
- Ensure it is snug but not overly tight, as this may affect the reading.
- Read the measurement at the point where the caliper or tape meets the rebar.
- Record the measurement in millimetres for accuracy.
It is advisable to measure multiple sections of the rebar to ensure consistency, as variations can occur during manufacturing.
Understanding the gauge of rebar is crucial not only for ensuring structural integrity but also for compliance with building regulations. The gauge, which indicates the diameter of the rebar, directly affects the load-bearing capacity of the concrete structure. For instance, a larger diameter rebar can support more weight, making it essential to select the appropriate size based on the specific requirements of the project. Additionally, different grades of rebar, such as Grade 40 or Grade 60, have varying tensile strengths, which further influences the choice of gauge.
Moreover, it’s worth noting that rebar is often coated with materials such as epoxy to prevent corrosion, especially in environments prone to moisture or chemical exposure. When measuring rebar that has such coatings, it is important to account for any additional thickness that may affect the overall gauge. This attention to detail not only enhances the longevity of the structure but also ensures safety and compliance with engineering standards.
Common Mistakes to Avoid
When selecting rebar gauge, several common mistakes can lead to issues down the line. Being aware of these pitfalls can help in making better decisions.
Overestimating Load Requirements
One of the most common mistakes is overestimating the load requirements. While it is essential to ensure that the rebar can handle the expected loads, opting for a significantly thicker gauge than necessary can lead to unnecessary costs and complications during installation.
Neglecting Environmental Factors
Ignoring environmental conditions can have detrimental effects on the longevity of the structure. Failing to consider factors such as moisture, temperature fluctuations, and exposure to chemicals can result in premature corrosion and degradation of the rebar.
Disregarding Local Codes and Standards
Local building codes are in place for a reason. Disregarding these regulations can lead to safety hazards and legal issues. Always consult local guidelines to ensure compliance and safety in construction.
Conclusion
Selecting the right gauge of rebar is a critical aspect of construction that should not be overlooked. By understanding the various factors that influence gauge selection, such as load requirements, environmental conditions, and project specifications, one can make informed decisions that enhance the structural integrity and longevity of concrete projects.
Investing the time to select the appropriate rebar gauge ensures that structures are safe, durable, and cost-effective in the long run. Whether you’re working on a small DIY project or a large commercial construction, the right gauge of rebar is essential for success.
In summary, understanding rebar gauges, considering relevant factors, and avoiding common mistakes will lead to better construction outcomes. With this guide, selecting the right gauge becomes a more manageable task, paving the way for successful and enduring structures.
Read more at: Why Reo Bar Is Essential for Reinforcing Concrete Foundations